In today's competitive manufacturing landscape, industrial robots have become indispensable tools driving efficiency and precision across production facilities worldwide. The automotive industry stands as one of the largest adopters of robotics technology, with major manufacturers leveraging automation to meet demanding production targets and quality requirements. From welding car frames to installing delicate electronics, robots perform critical tasks throughout the vehicle manufacturing process, ensuring consistency while reducing production time and costs.
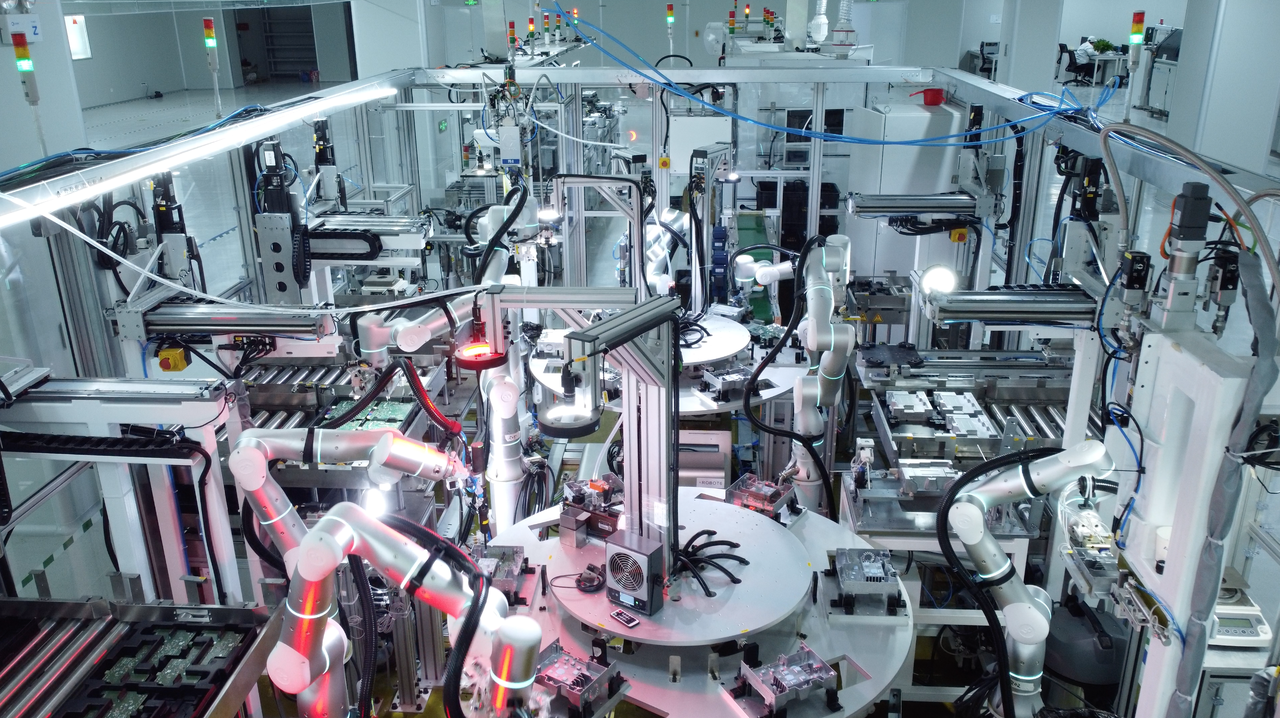
The Evolution of Industrial Robots in Automotive Manufacturing
The journey of industrial robots in automotive manufacturing began in the early 1960s when General Motors introduced the first industrial robot, Unimate, to its production line. Initially performing simple tasks like spot welding, these early robots operated in isolation from human workers.
The 1980s and 1990s saw significant technological advancements as robots gained improved sensors and more sophisticated controllers, expanding their application range to more complex tasks. Japanese automakers particularly embraced robotics during this period, establishing new standards for manufacturing efficiency.
Recently, the emergence of collaborative robots or "cobots" has created new possibilities for human-robot teamwork. Flexiv's adaptive robots represent the next evolution in this journey, seamlessly fusing industrial-grade force control with advanced artificial intelligence to adapt to complex environments in much the same way humans do.
Key Applications of Industrial Robots in the Automotive Industry
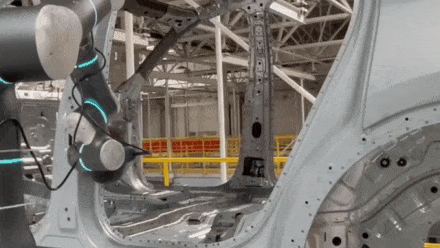
Deburring and weld grinding are critical post-processing steps in automotive manufacturing, ensuring smooth surfaces and eliminating sharp edges that could compromise part quality. Industrial robots equipped with force-sensitive grinding tools can adaptively remove excess material while maintaining consistent pressure, even on complex curved surfaces. Flexiv’s force control technology enables real-time adjustments based on material hardness and weld seam variations, improving precision and reducing rework. Automated robotic systems also enhance worker safety by handling this labor-intensive and potentially hazardous task, minimizing exposure to metal dust and repetitive strain injuries.
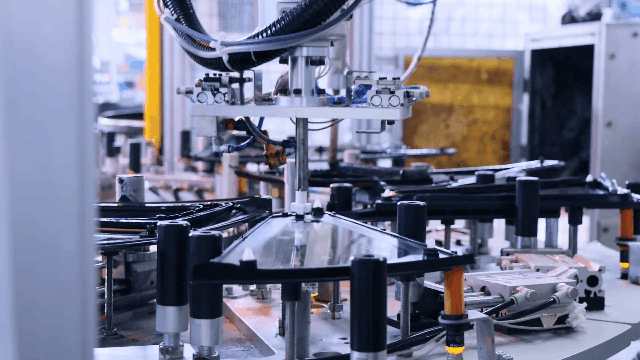
The adhesive primer application requires high precision to ensure proper bonding strength and corrosion resistance in automotive assembly. Robotic systems excel in dispensing primers with exact thickness and coverage, even on contoured surfaces or hard-to-reach areas. By automating this process, manufacturers eliminate inconsistencies caused by manual application while reducing material waste. Robots equipped with vision systems can detect surface irregularities and adjust primer deposition accordingly, ensuring optimal adhesion. Additionally, automation protects workers from prolonged exposure to volatile organic compounds (VOCs) and other hazardous chemicals used in primer formulations.
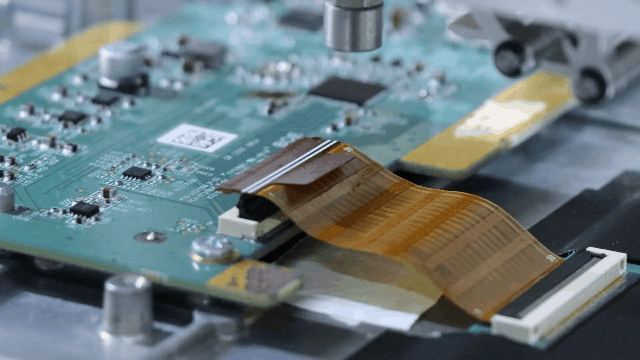
Assembly operations increasingly rely on robotic systems to install components ranging from heavy powertrain elements to delicate electronic modules. The Flexiv adaptive robots bring particular advantages through their advanced force sensing capabilities, allowing them to handle delicate components and adjust to part variations without reprogramming.
Quality inspection robots can inspect components with unwavering attention to detail, detecting defects invisible to the human eye and ensuring 100% inspection coverage with sub-millimeter precision.
Benefits of Using Industrial Robots in the Automotive Industry
The implementation of robotic systems delivers numerous advantages that directly impact productivity, quality, and operational costs. Robots can operate continuously without breaks or fatigue, dramatically increasing production throughput with many manufacturers reporting productivity increases of 30% or more.
Enhanced precision represents another significant advantage, with modern industrial robots achieving positional accuracies measured in fractions of a millimeter, ensuring consistent quality across millions of repetitions. Flexiv's force-controlled robots add another dimension by regulating not just position but also the forces applied during assembly operations.
Improved safety has become increasingly important as manufacturers focus on reducing workplace injuries. By taking over dangerous tasks involving extreme temperatures or heavy lifting, robots significantly reduce injury risks.
Cost savings provide the business case for robotic implementation, with manufacturers typically seeing returns through reduced labor costs, decreased material waste, lower warranty claims, and improved production efficiency.
Future Trends and Innovations in Automotive Robotics
Artificial intelligence and machine learning represent perhaps the most transformative technologies impacting automotive robotics. Advanced algorithms enable robots to optimize their movements and even improve performance over time through experience. Flexiv stands at the forefront of this revolution with robots incorporating sophisticated AI systems.
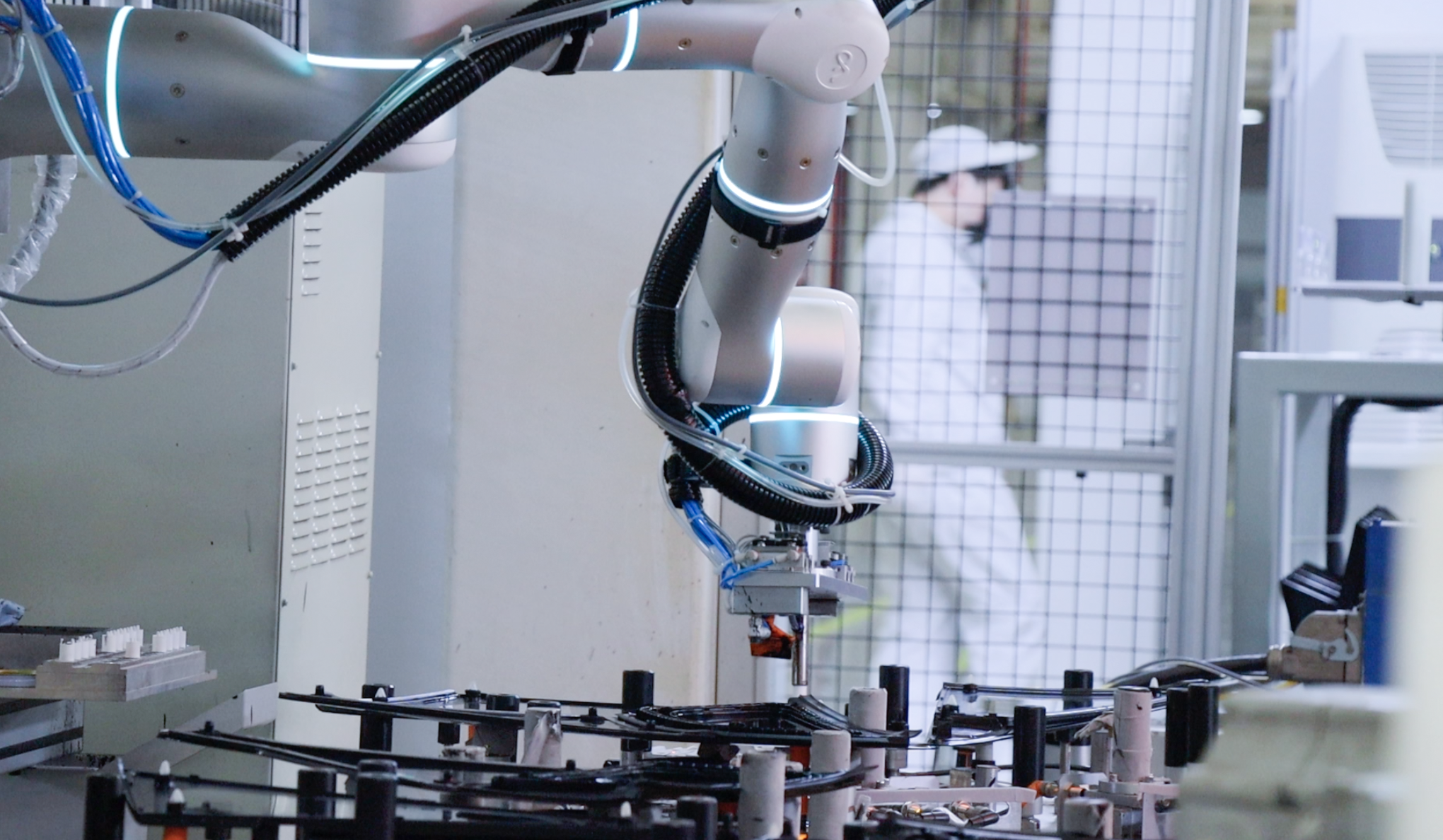
Adaptive robots designed specifically for complex, variable tasks represent another significant trend. Unlike conventional industrial robots that require precisely positioned parts, adaptive robots can accommodate variations in component positioning. The Flexiv Rizon series exemplifies this approach, combining advanced sensors with AI-powered control systems to handle operations that previously required human dexterity.
The future of automotive manufacturing will likely see increasingly intelligent and flexible production systems, with robots handling a wider range of tasks while adapting to changing vehicle designs and production requirements. As electric vehicles gain market share, manufacturing flexibility becomes increasingly important, making advanced robotic systems that can be quickly reprogrammed essential in this dynamic environment.