Case Study

Agricultural
Automated Fish Fillet Shaping Solution

General Industry
Automated Shutter Sanding

Consumer Electronics
Adaptive Robotic Keyboard Testing
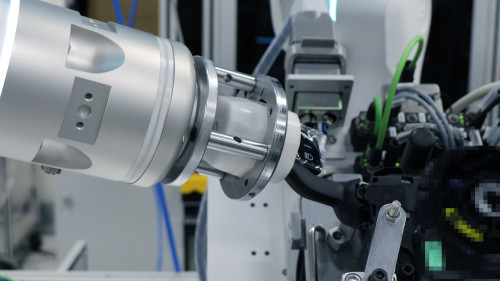
Automotive
Automotive Signal Switch Calibration

Consumer Electronics
Automated Voice Coil Assembly for Audio Devices
We offer solutions to diverse customers









